
Kurvestol
Furniture epitomizes the shaping challenge of designers; the shape of furniture relates directly to the body, and the quality of this shape is immediately assessed by the body, all details being seen and felt. As a design object, furniture is mobile by definition, but the space it creates alone or in unison with other pieces of furniture engages in a continuous dialogue with the architectural context, thus furniture can not be evaluated as isolated pieces.
Kurvestol is a flexible, lightweight chair that adapts to your body without complex mechanisms.
The use of traditional Danish crafting techniques--steam-bent rattan, with curves set by flame--combines with an open structure to create an inviting, comfortable armchair with a material callback to early 20th-century designs. As an object the chair is familiar because of its material, but modern because of its shaping.
Kurvestol is made from just 5 pieces of rattan-a super lightweight, fast growing grass- joined with dowels and wrapped with rattan strips. The minimal structure and traditional joints mean that the chair has an inherent flexibility and movement.
Project: Furniture 1:1 (Master's Studio)
Location: Kunstakademiets Arkitektskole, Copenhagen
Year: 2010
Instructor: Nicolai de Gier

Kurvestole in situ

Design Process
Sketching and prototypes through sketch modelling progressed by studying both desired postures, existing designs and traditional cane shaping techniques.
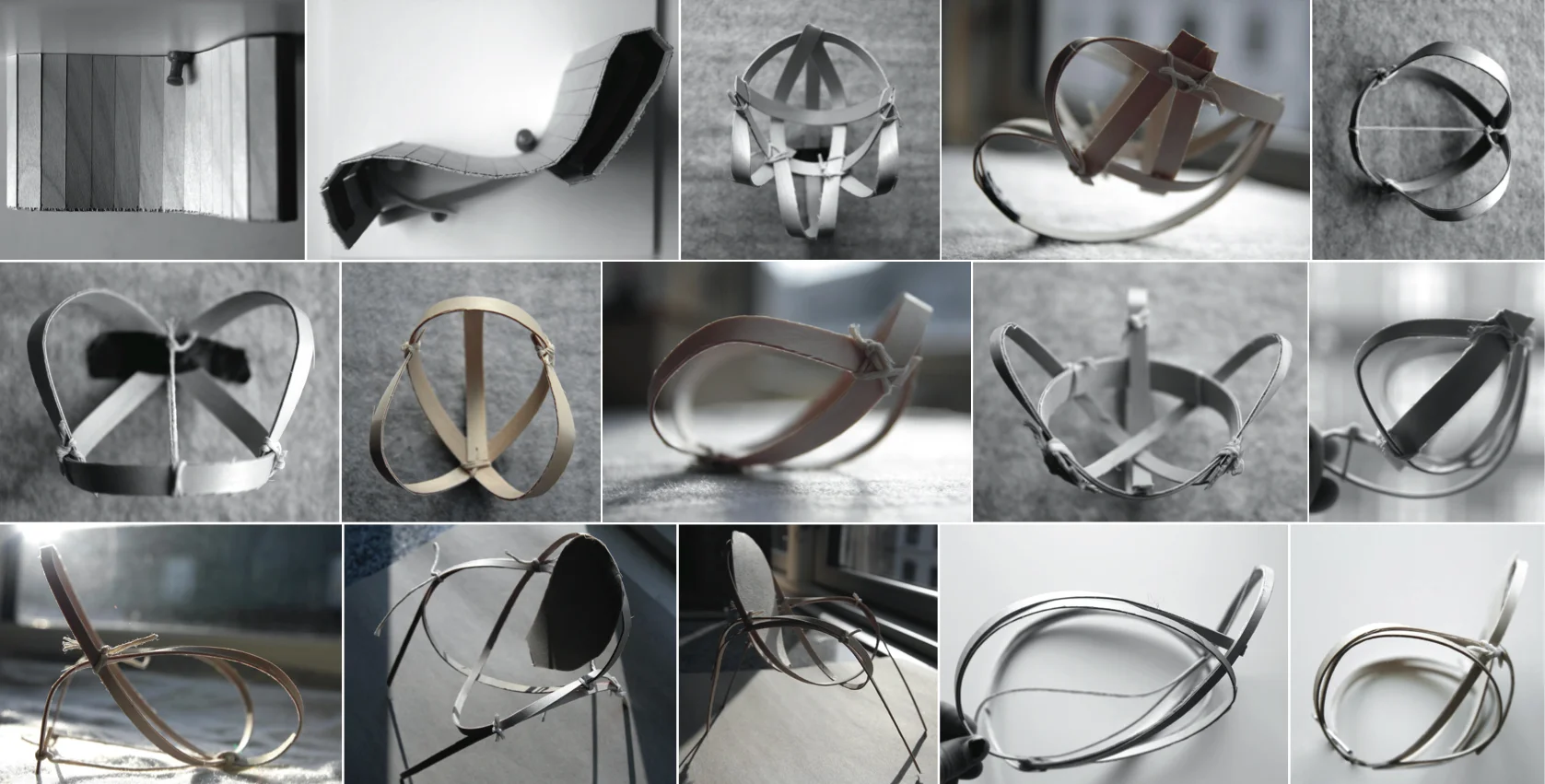
Sketch models

Prototype 1
At a scale of 1:5, the first prototype was a rough shaping guide that would help direct the form of the first 1:1 prototype in the actual material of rattan.

Procedure & Production Issues
While producing the first 1:1 prototype I ran into several issues in shaping, bending and strengthening the frame which needed to be resolved in the next iteration.

Process - Prototype 3
Learning from the first 2 prototypes, I worked the bent rattan into a mold to ensure that both sides of the chair would contain the same bends. The completed frames then had to be joined using traditional dowels and cane wrapping techniques to hide the joints. No glues or fasteners were used.

Joint Detail
The crux of the two outer structural frames had to be carefully bent and joined using a dowel and traditional cane wrapping. The triangular joint was used for structural strength that would still maintain a light and airy form.

Completed Prototype
The 3rd prototype was structurally sound and was designed to accommodate a felt lining that would create comfortable cushioning without a lot of padding and without distracting from the frame.

Structural Test

Completed Prototype
Kurvestol was a success as a lightweight, comfortable and flexible piece of furniture, but unfortunately did not fold down into a suitcase. The fate of kurvestol is unknown but was last seen in the courtyard behind a building on Ægirsgade.